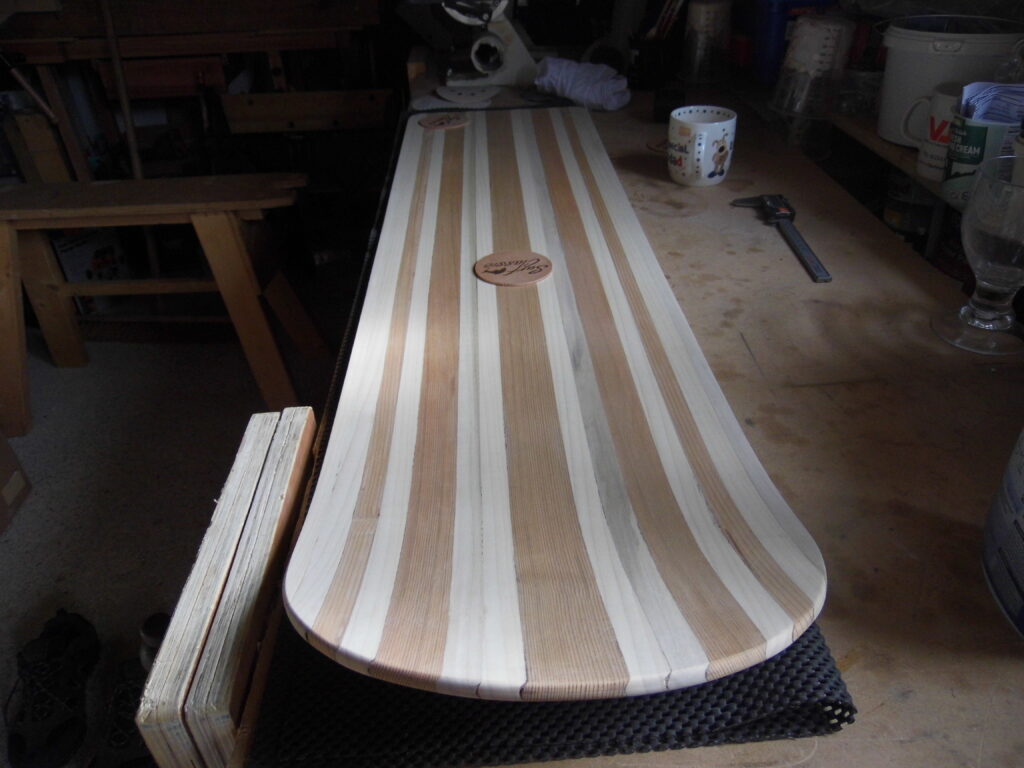
Well, I’ve had this piece of Great Western Memorabilia on my wall for ever.
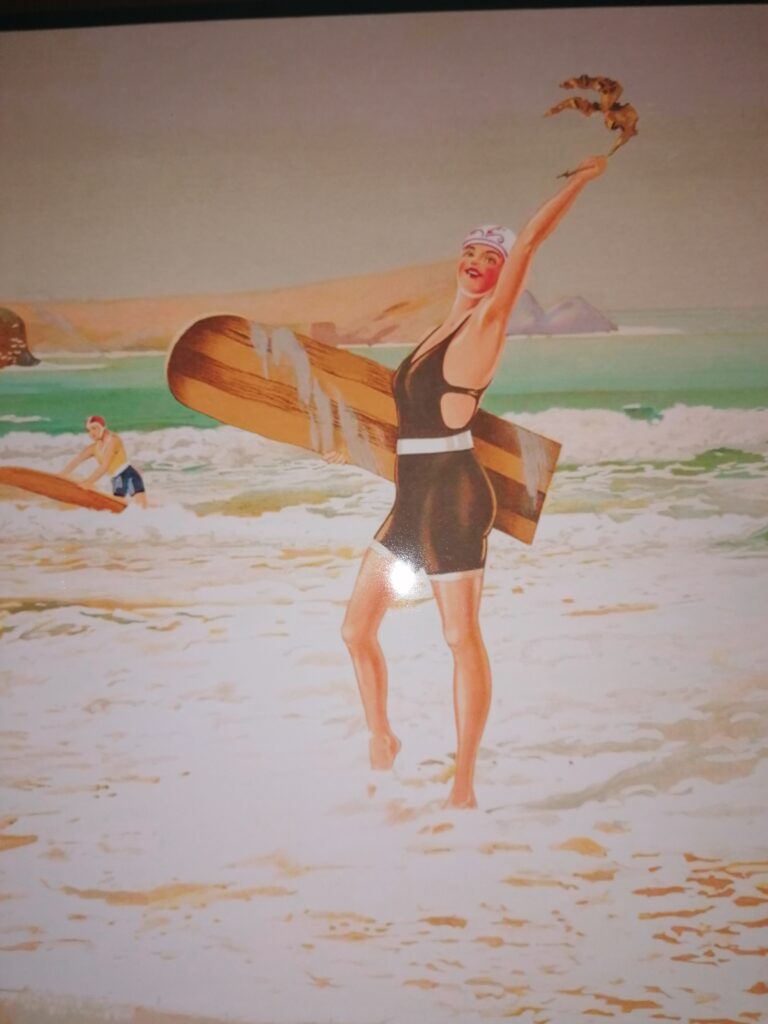
The bathers all appeared to be having so much fun….and not a wet suit in sight, that I thought why not have a Surf Classic™ version of a traditional timber plank board?
Build Brief
Reclaimed or sustainable hardwoods to be used
Must be the Lightest and strongest in class, finished weight only 1.72 kg
Must be formed on the Ken’s original 1961 Briereley Steam Press
Great in the surf and also a beautiful piece of surf Wall Art for the other 50 weeks of the year.
Manufacturing
The initial board and its jig modifications have taken a little over 4 months to design and construct working at home outside my normal production schedule, and given me some fair challenges along the way ultimately great joy seeing it through to fruition.
This is its story
Modifying my venerable 60+ year old original North Cornish Electro-Steam Press to accommodate the bending of 30 pieces of varying strength hardwoods required us creating a larger timber infeed and re-designing and manufacturing an additional steam generator to provide the increased volume of steam now required.
In case you’re wondering the base Aluminium former used for the curve here is part of a Front-Line millitary aircraft fuel drop tank circa 1957and was re tasked in 1960 by the press’s original maker Top Bloke and gifted Cornish engineer Ken Brierley.
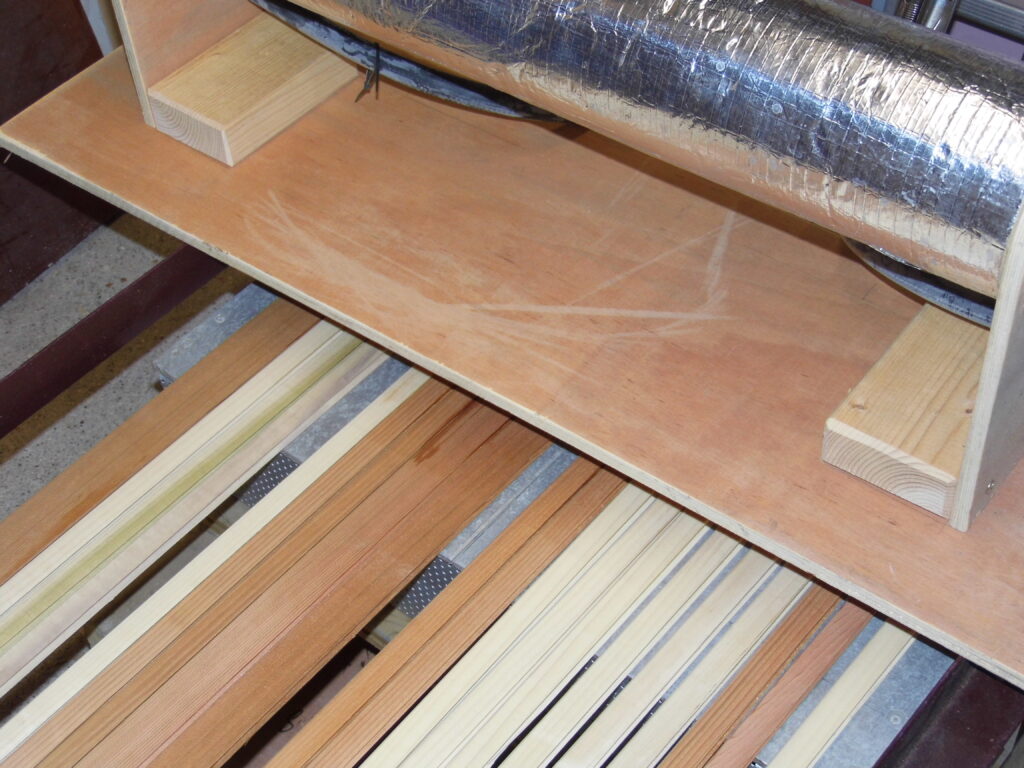
A defunct cold former served well for gluing the bead & cove strip planks
Timber snail cams gave lateral pressure and the strong backs hold the planks true whilst the glue cured.
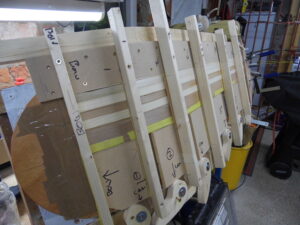
After cleaning and sanding it smooth instead of the usual “Surf Classic™” Logo burnt in with our copper branding iron this special has a trademarked inlay.
Challenges along the way
As with all things experimental particularly when juggling those three critical elements of weight, strength and beauty, there is usually a shortcoming.
In this case, it was its torsional strength allowing the board to bend beyond normal limits along its axis.
Challenge
The limited shear strength of the central 12mm Red Cedar plank was a possible weakness for axial strength with it possibly breaking along the grain under stress.
Solution
4oz Fibreglass was used to strengthen the board surfaces, this may have compromised its overall weight but as its initial weight was less than a kilo (942g) it still finished out at only 1.72Kg which is still less than conventional plywood boards of the same size.
The Future
We will be scaling up and manufacturing these boards in 2022 we think they will be a great addition to our range.
Designed and made our own Cauls (4 way clamp)
We will be sourcing and milling over 50% of our timbers for strip plank boards from reclaimed hardwood.
The Cedar and Mahogany on the prototype came courtesy of a school laboratory demolition and American Poplar strips are essentially offcuts from a professional Boat Builder.
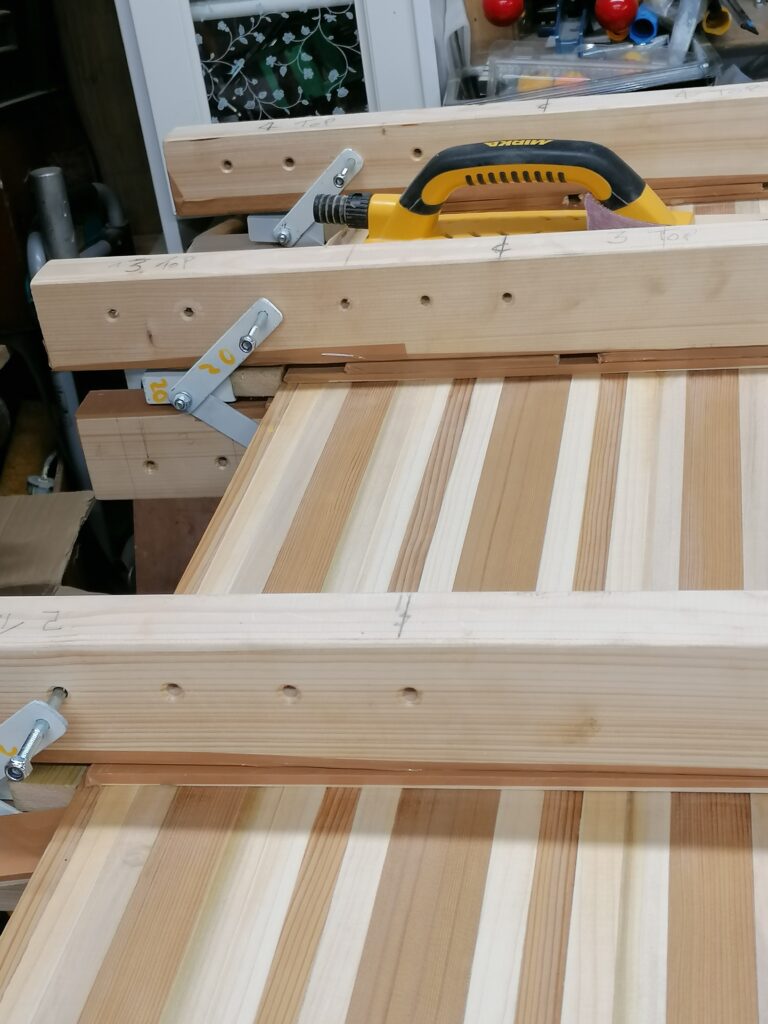
Build Information
Timber 12mm Paulownia with Bead &Cove, 12 mm Red Cedar with B&C, 12mm American Poplar (Tulip Wood) with green and cream graining B&C
Sustainable timber and Fibre Glassing materials -sourced from Phil at Fyne Boat Kits www.fyneboatkits.co.uk
Preparation and final professional surface finishes -P101Clear from Teal and Mackrill www.teamac.co.uk
Glassing guidance from Dave Butler professional Boat Builder www.butlerboats.biz
Silver Paddleboards web site was a mine of information for designing the clamps.
Paul Fishers book “Strip Plank Boat Construction” ISBN :978-1-898909-18-7 has provided all the information we could have wished for and whetted our appetite for designing a proto hollow board that will provide additional buoyancy and open up life beyond the breakers (watch this space)
Thank you for taking time to view this article, please use the contact page for any queries or information you may require.